CoBlast technology combines blasting and coating in one process step
- One-step, ambient temperature, ambient pressure process
- Process compatible with wide range of corrosion resistant coatings
- Applications: from foils and wires to complex 3D shapes
The CoBlast process of company ENBIO is a one-step, ambient temperature, ambient pressure process that uses conventional grit/micro-blasting equipment to remove a metal’s natural oxide layer and replace it with a desired functional Skin. Abrasive and coating powders are simultaneously blasted onto the metal surface from a single nozzle. No wet chemicals are involved. The abrasive mechanically abrades the substrate, exposing active chemical bonds to which the coating particles bond before an oxide layer can reform. The inert nature of the abrasive ensures that it does not easily form chemical bonds, so that the process forms a coating with very good coverage, with little or no abrasive remaining on the surface or embedded in the substrate.
Applications: from foils and wires to complex 3D shapes
CoBlast Skins can be applied to almost any substrate geometry, as the nozzle is easily mounted on standard industrial robots and other automation equipment. Typical applications include complex 3D shapes, flat plates, tubes, foils and wires. Suitable substrate materials include titanium, stainless steel, mild steel, aluminium, magnesium, nitinol, inconel, cobalt chrome and bulk metallic glass, among others.
CoBlast skins are typically 2-5 microns thick, meaning that fine surface details are preserved after coating. The abrasive and coating materials, and the process parameters, can be tailored to coat delicate parts with minimal mechanical or thermal damage. Skins have been applied to titanium foils as thin as 25 microns, and to delicate structures including stents and metal foams.
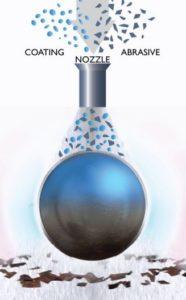
Process compatible with wide range of corrosion resistant coatings
The company is developing corrosion resistant coatings with the aim of matching the performance of zinc-rich paint primers, with the process efficiency and environmental benefits of CoBlast. Several corrosion resistant coatings including zinc phosphate, magnesium phosphate, and cerium oxide can be deposited using CoBlast, with no VOC content and minimal waiting time before the application of a topcoat. Hydrophobic Skins in development have reached water contact angles of 150° and hysteresis <10°. CoBlast Skins have achieved a coefficient of friction below 0.15, as measured by the pin-on-disk method. These coatings exhibit significantly reduced wear compared to the untreated substrate.